Processing Technology
Tempering
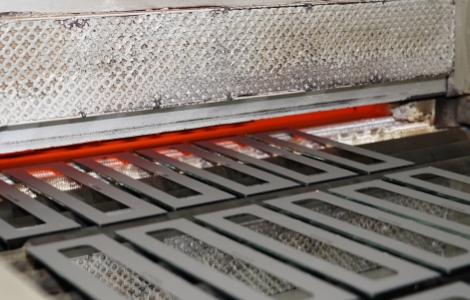
Thermal tempering
The glass is heated to near the softening point, then by blowing room temperature air on both sides it is rapidly cooled, A compressive stress layer is formed near the surface. By forming this compressive stress layer, The strength of glass is 3~5 times higher than that of normal glass. The characteristics of tempered glass are that when breaking, partial break does not occur, The whole glass crumbles into fine granules. Fragments does not become large one and are relatively non-sharp. Therefore, it is also characterized by relatively safe glass.
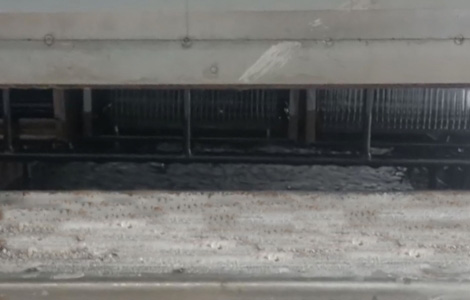
Chemical tempering
Chemical strengthening is a method of increasing the strength of glass by scientifically forming a stress layer on its surface. When the glass is immersed in a potassium nitrate solution heated to around 380 degrees, the sodium present on the surface of the glass is replaced by ion exchange with potassium in liquid. due to the different atomic radii of sodium and potassium, A stress layer of 10~20 microns is formed on the glass surface. Processing time is about 1 hour. Chemical strengthening is mainly used for thin glass, and is applied to smartphone cover glass and so on.
Coating
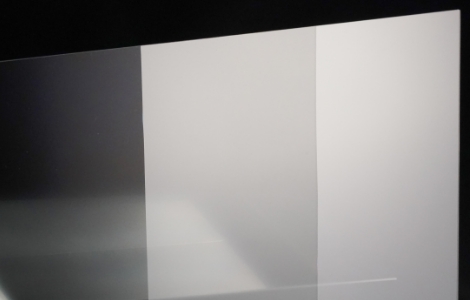
AG coating
AG (Anti-Glare) coating is a process that reduces surface reflections. By making very fine irregularities on the surface of the glass, it can be diffused the reflected light to reduce reflections.
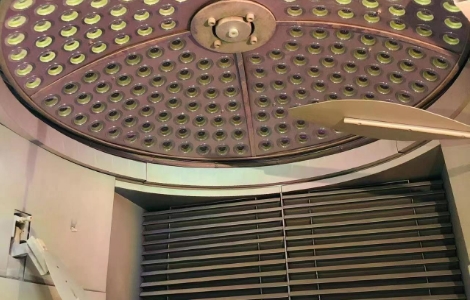
AR coating
AR (Anti-reflection) coating is to prevent light reflection, and is used on glass plates, eyeglass lenses, computer displays, liquid crystal And so on. AR coating method is to make many film layers on the glass to reduce the reflection on the surface. In the vertical incidence light, the reflectance is around 0.5~2%.
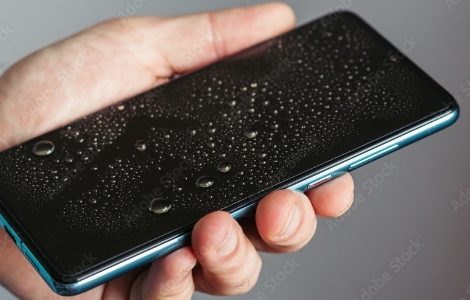
AF coating
AF (anti fingerprint) coating prevents water and oil stains by repelling the surface of the glass. The fats and oils dirt adhered to the glass surface can be easily wiped off.
Printing
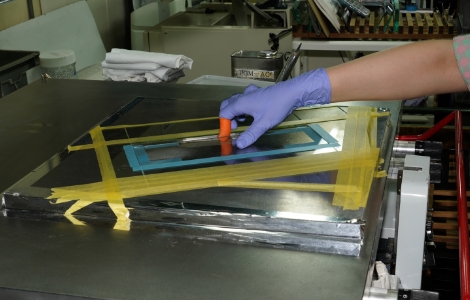
Organic printing
Printing on glass is performed using a room-temperature curable resin ink that can be mixed in color. After printing, it is hardened at 200°C or less. It has high adhesion to glass, and the hardness of the ink is 3H~4H. It is also possible to print on mirrors with special printing for interior decoration. It cannot be used for exterior use. Organic inks are used for smartphones and tablets.
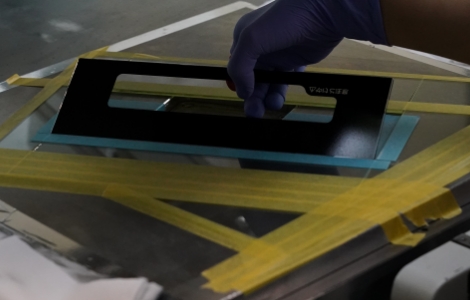
Inorganic printing
Glass printing using inks are mainly composed of glass powder and inorganic pigments. After printing, following volatilization and drying of the solvent, it is heated at a high temperature of 600°C or higher, and the ink is fused to the glass. Through this process, the glass and ink are fused. The ink does not peel off easily and the color does not fade easily. The hardness of the ink is about 6H. It is often used for decoration such as printing logos and letters on the glass of equipment that gets hot like microwave oven, oven, etc., It can be used for both interior and exterior but it may become discolored depending on the usage environment. In environments containing hydrogen sulfide gas, such as hot spring resorts, it cannot be used.
Bending
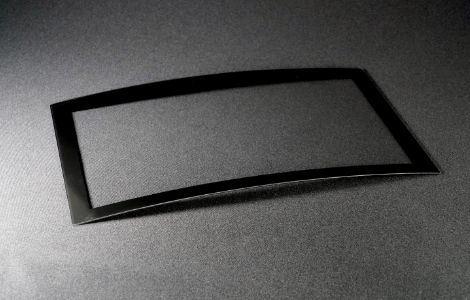
Bending
Bending glass is made by thermal process. After flat glass is cut and chamfered, that is installed in molds with predetermined curvature, then it is placed in a high temperature furnace. The heat causes the glass to bend along the shape of the mold.
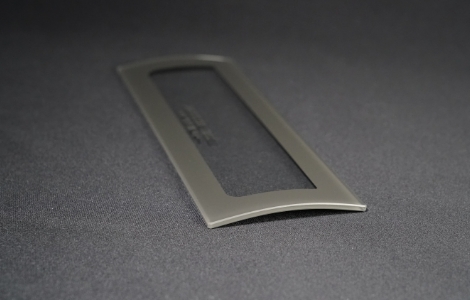
Tempered bending glass
Tempered Bending glass can be made by thermal bending process and following blowing process.
Surface polishing
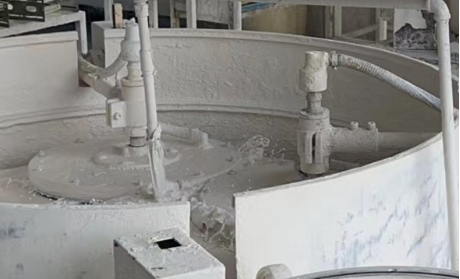
Surface polishing
A disc-shaped polishing machine is used to polish the surface of the glass with the addition of cerium oxide. It is possible to make fine surface scratches less noticeable by polishing the surface.
Processing of glass edge
Safety Chamfering
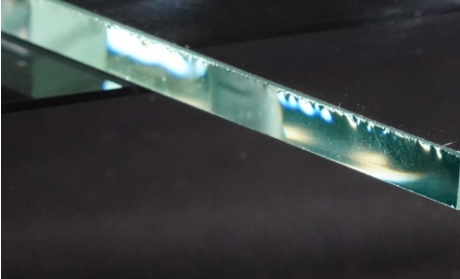
The sharp edges of the cut glass are ground down with a grinder to a degree that prevents hands from being cut.
Rough Grinding
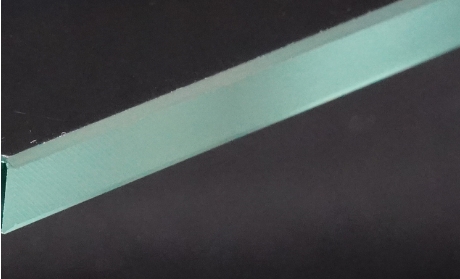
The sharp angles and sides are polished using a machine.
Gloss Polishing
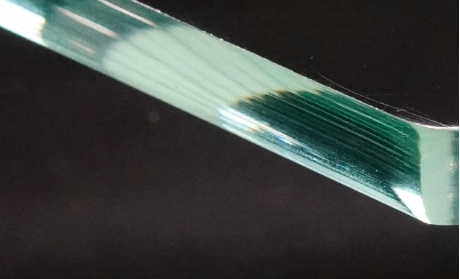
This is a process of polishing the cut edges of the glass to give them a glossy finish.
C-Cut
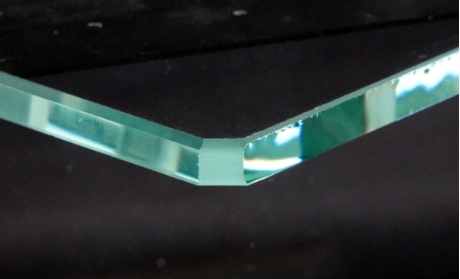
R-Cut
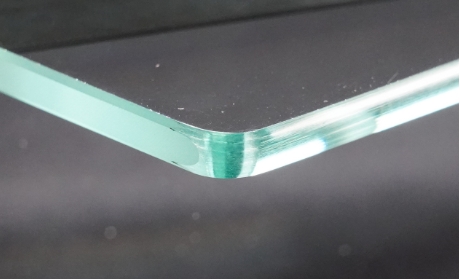
The corners of the glass are rounded off.
Kamaboko
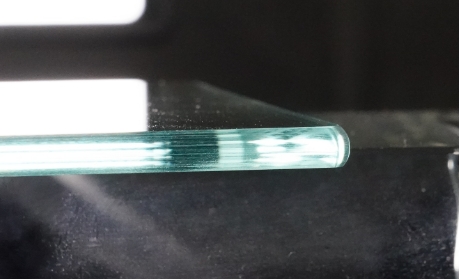
The cut sides of the glass, which become the edges, are rounded off and polished.